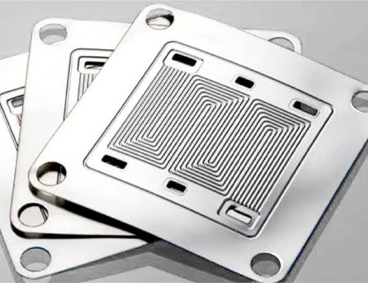
Bipolar Plates
Bipolar plates play a crucial role in enabling clean and efficient power generation across a wide range of applications. Acting as conductive pathways, these plates facilitate the flow of hydrogen and oxygen, ensuring efficient electricity generation. Moreover, the quality and precision of bipolar plate manufacturing directly impact the efficiency, reliability, and longevity of PEM fuel cells.
Here at Trihyd, we specialize in designing, manufacturing, and distributing high-quality bipolar plates. Through effective design, we cater to the demands of various fuel cell applications. We prioritize innovation and precise engineering. We use lightweight materials and advanced coatings. Our goal is to deliver reliable, cost-effective solutions. We design bipolar plates to enhance fuel cell efficiency, durability, and environmental sustainability.
Now, let’s delve into the specifications of bipolar plates
Material
Typically, bipolar plates are crafted from conductive materials such as graphite, metal alloys like stainless steel, carbon composite materials, or polymers doped with conductive fillers. Each material boasts its own set of advantages and disadvantages concerning conductivity, corrosion resistance, weight, and cost. Consequently, selecting the appropriate material is essential to align with specific business needs.
Thickness
The thickness of a bipolar plate significantly impacts its performance. Hence, the thickness can vary depending on the specific fuel cell application and manufacturing process chosen. For instance, thinner plates effectively reduce weight and volume, while thicker plates may offer superior mechanical strength and durability compared to thinner alternatives.
Surface Treatment/Coating
Manufacturers often apply surface treatments or coatings to bipolar plates to enhance corrosion resistance, gas diffusion, and minimize contact resistance. Such treatments not only prolong the lifespan of the plates but also enhance overall fuel cell efficiency.
Flow Field Design
Flow field patterns within bipolar plates optimize the distribution of hydrogen and oxygen across the electrode surface. Common designs include serpentine, parallel, interdigitated, and combination patterns, each offering unique advantages in terms of mass transport and pressure drop. Thus, selecting the appropriate flow field design is crucial for maximizing fuel cell performance.
Compression and Sealing
Ensuring proper compression and sealing is vital to prevent gas leakage and ensure efficient ion transport within the fuel cell stack. Gaskets or sealing materials are utilized to create tight seals between adjacent plates, while compression mechanisms apply the necessary pressure to maintain contact between the plates and membrane electrode assemblies (MEAs), ensuring optimal performance.
At Trihyd Technology, we address all your requirements and needs comprehensively. For all your bipolar plate needs, feel free to reach out to us today!.