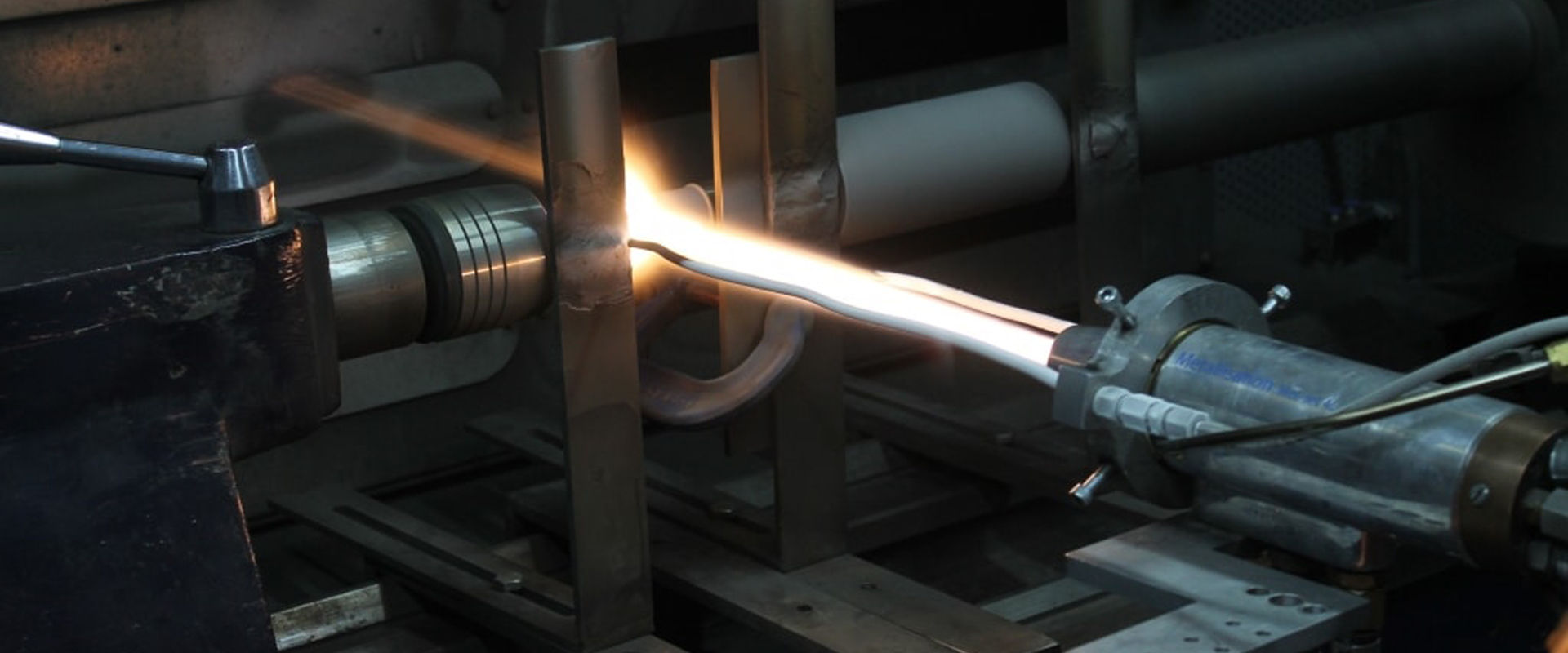
Wire Spray Coatings
Thermal spray coatings, also known as Wire spray coatings, provide highly scalable applications to substrates of various sizes, shapes, and geometries, including complex and irregular surfaces. Additionally, they offer versatility in coating deposition, making them suitable for a wide range of industrial applications. Wire spray coatings or thermal spray coatings, involve the process of applying a protective layer onto a surface using a high-velocity stream of molten or semi-molten material. Opt for our wire spraying technology to safeguard your assets with a seamless, resilient shield. If you want to protect your assets, equipment, industrial machinery, or critical infrastructure of your business, then opt for our coating services that stand as guardians against corrosion, wear, and environmental degradation. Furthermore, our coatings offer long-term protection, thereby ensuring the uninterrupted operation of your assets and reducing overall maintenance costs.
Now you don’t need to worry about the life of an asset because now you can protect and make the asset live longer with the help of wire spray coatings. Therefore, contact us today and ensure the longevity and durability of your valuable assets.
Process
Material Feeding
material feeding is the first step in wire spray coating process. A wire of the coating material, typically metals or alloys, is fed into a thermal spray gun. This wire ensures continuous feeding of material to spray gun.
Heating
Using a combustion flame, plasma arc, or electric arc, the wire heats up, melting the material into a semi-liquid state, making it easy to spray onto any surface.
Atomization and Propulsion
In this step, the melted material is converted into fine droplets or particles, aiding in achieving the desired fine finish after spray coating. This transformation is facilitated by compressed air, inert gas, or a combination of both.
Coating Build-up
In the coating process, the final stage involves spraying a fine layer of melted material through a spray gun. Multiple passes may be made to achieve the desired coating thickness.
Types of Wire Spray Coatings
Metallic Coatings:
Typically this type of coatings consists of metals or metal alloys such as aluminum, zinc, nickel, or stainless steel. These coatings provide corrosion protection, wear resistance, thermal insulation, or electrical conductivity.
Ceramic Coatings
Made from ceramic materials like alumina, zirconia, or chromium oxide. Ceramic coatings offer thermal barrier properties, erosion resistance, and high-temperature protection.
Composite Coatings:
Combining metallic and ceramic materials to achieve specific properties such as enhanced wear resistance, thermal conductivity, or surface hardness
Applications
Corrosion Protection
Industries such as marine, oil and gas, and infrastructure primarily utilize wire spray coatings to protect metal structures from corrosion. Moreover, these coatings provide a durable shield against environmental elements, thereby enhancing the longevity of the structures. Additionally, they contribute to cost savings by reducing the need for frequent maintenance and repairs.
Wear Resistance
Components subject to wear and abrasion, such as industrial machinery, automotive parts, and aerospace components, benefit from wire spray coatings to prolong service life. Furthermore, these coatings enhance performance and durability, thereby reducing maintenance costs and downtime.
Thermal Barrier Coatings
Thermal insulation and heat management are provided by ceramic wire spray coatings. Moreover, these coatings offer exceptional resistance to high temperatures.
Electrical Insulation
Certain wire spray coatings insulate electrical components and prevent short circuits.
Advantages
Versatility
Business entities adopt wire spray coating at large because it offers versatility, allowing application to a wide range of substrates, including metals, ceramics, and polymers.
Cost-Effectiveness
Compared to traditional coating methods, in which technology was not much used, wire spray coatings offer a cost-effective solution. At Trihyd, we offer cost-effective technology-based services.
High Deposition Rates
The process allows for rapid deposition of coatings over large areas, making it suitable for industrial-scale applications. Industrial machines or equipment can apply layers of coatings more quickly, thus accelerating the process compared to traditional coating techniques. Consequently, this method is less time-consuming.
Customization
By selecting different coating materials and process parameters, manufacturers can tailor the properties of wire spray coatings to meet specific performance requirements. Additionally, this flexibility allows for customization based on individual needs.
Resulting Properties
- High thickness buildup and high coating rates are possible
- Strong adhesion
- Uniform coating and good density
- Process of choice for high-volume coating of metal alloys
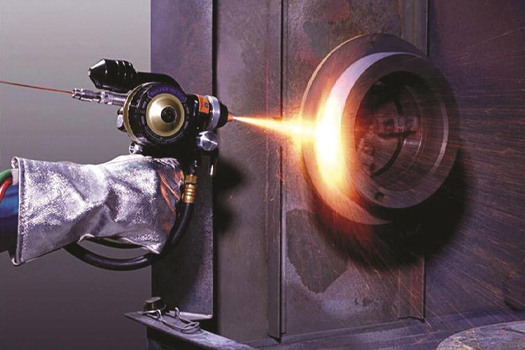
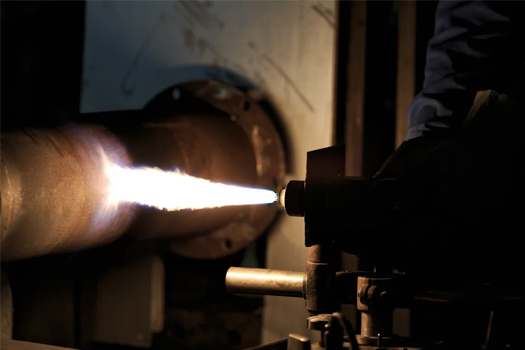